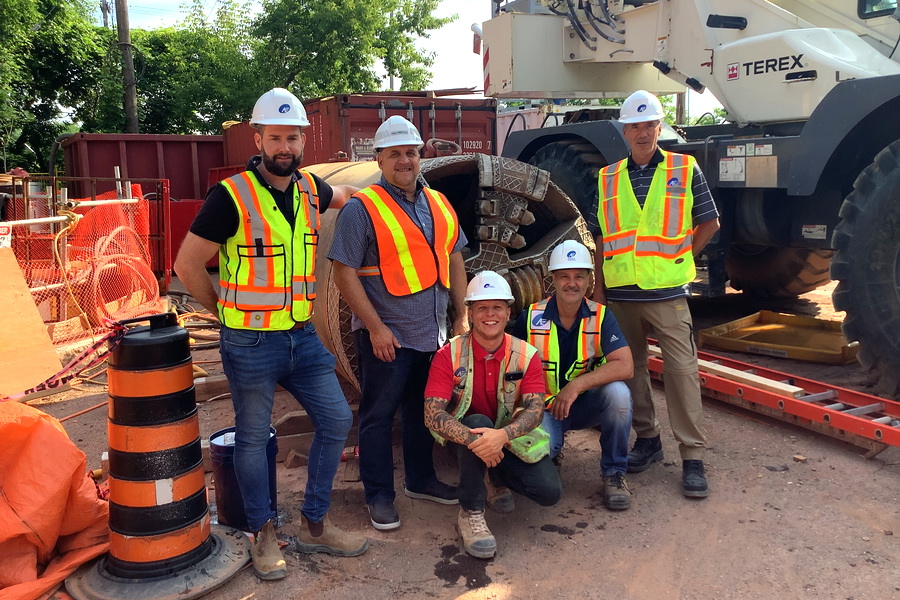
Cian McDermott’s journey to become a civil engineer and now Manager of the Civil Infrastructure group in our Niagara-on-the-Lake office, began many years ago in his native Ireland. From an early age, Cian was always interested in construction and how things were put together. He recalls that his favourite toy as a child was the construction building set, Meccano.
As a high school student, Cian worked on construction sites and built houses every summer. Cian recalls, “One early morning on a wet and windy summer day, we had a full day ahead of us pouring concrete foundations. However, before we could begin, we waited 30 minutes for the civil engineer to arrive and sign off on the foundation subbase. Eventually, the engineer arrived, approved the foundation, and drove away. I then had to shovel concrete for the next 12 hours in the rain. This was the moment that I decided I wanted to become a civil engineer.”
Cian shares that his family has always been a positive influence on him. His parents taught him the value of working hard, and always balancing work with life. Cian tells us, “My dad managed our football teams when I was growing up. Through sports, he taught me about teamwork, looking out for your friends, and having fun.”
In 2010, Cian emigrated to Canada and began his career at Associated Engineering as a junior site engineer. Cian says, “I liked that Associated was a mid-sized firm competing with much larger companies. The range of projects that Associated was completing was of particular interest to me. The company has provided me with the framework and mentorship to succeed.”
“The culture at Associated is a great fit for my personality and skills.”
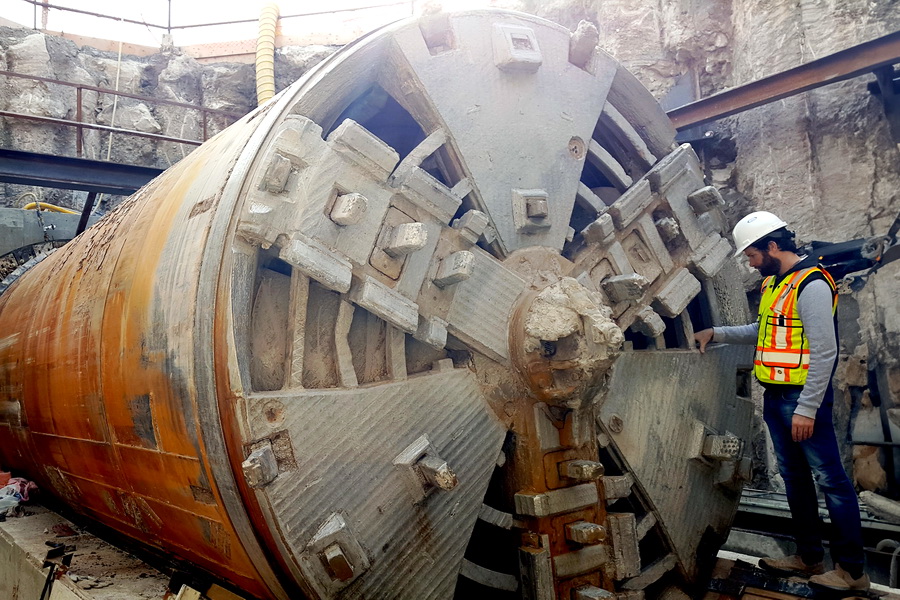
The first Associated project Cian worked on was the Avenue Road Watermain in Toronto, under the supervision of Mark Belanger (Division Manager, Infrastructure). Cian remembers how Mark always made himself available to answer questions and walk him through the thought process of his designs, which Cian has always appreciated. Cian advises, “The watermain was located in a completely different, busy urban environment from what I was used to working on in Ireland. The Avenue Road Watermain remains my most memorable project for its complexity and large-scale, and the opportunities it provided to me as a young professional.”
In the first ten years of his Associated career, Cian describes he has had the opportunity to work on many challenging and interesting projects.
“I’ve designed large diameter watermains through urban and rural settings, completed the design of large diameter sanitary infrastructure with microtunnel technologies, and worked as a contract administrator, resident engineer, and project manager.”
Cian tells us, “I am grateful to work for a company that provides young aspiring engineers with the opportunities to develop their skills, while working on complex projects and getting exposure to collaborating with contractors and clients.” Cian enjoys the diversity and range of projects that can be experienced as a civil engineer and how no two days are the same in consulting engineering.
Now, as a manager, Cian believes it is important that all members of the team feel that their opinions and ideas are being heard and considered. “There are many different personalities involved with every project, so it’s important to understand each team member’s strengths and passions and position everyone to generate the best results for the project and client. It’s important to foster a working environment that allows everyone on the team to flourish and feel they are making a significant contribution to the project.”
Cian tell us that mentoring staff is extremely important and young staff receive guidance and have a go-to person to help them daily. “In my opinion, from a learning perspective, the pandemic was the hardest on our newly-hired graduates, as they missed the office culture and that opportunity to learn from being around other engineers and staff.”
Cian advises young people entering consulting engineering to keep an open mind and be open to any learning opportunity that comes their way.
“Communication is key – the more the better. If you need help, reach out. Also, be a team player and listen, as there is always something to be learned from others. Lastly, be accountable for the work you are assigned and complete.”
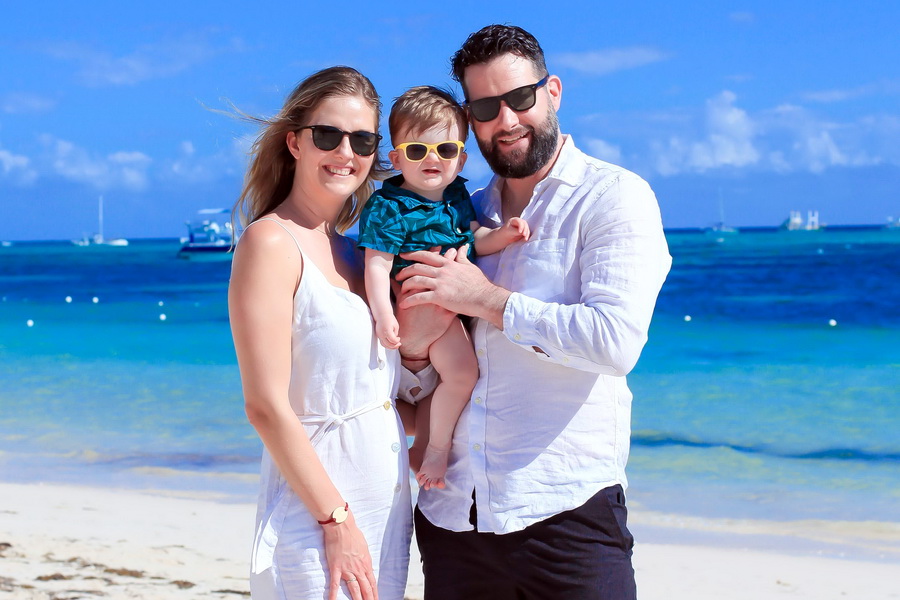
Outside of work, Cian enjoys spending time with his family and friends, playing sports, cooking, attending sporting events, and travelling the world.