In the next episode of AE Live, Kent Eklund, Senior Vice President, Transportation discusses his experience in transportation. Kent explains how transportation planning has changed over the years, and how the availability of information has revolutionized how planners determine municipal development. He also shares his thoughts on some major projects going on across Canada, and how light rail transportation and bus rapid transit are important for the future growth of cities and managing traffic flows on existing infrastructure.
Month: July 2024
Sponsoring and presenting at UESI Pipelines 2024 Conference
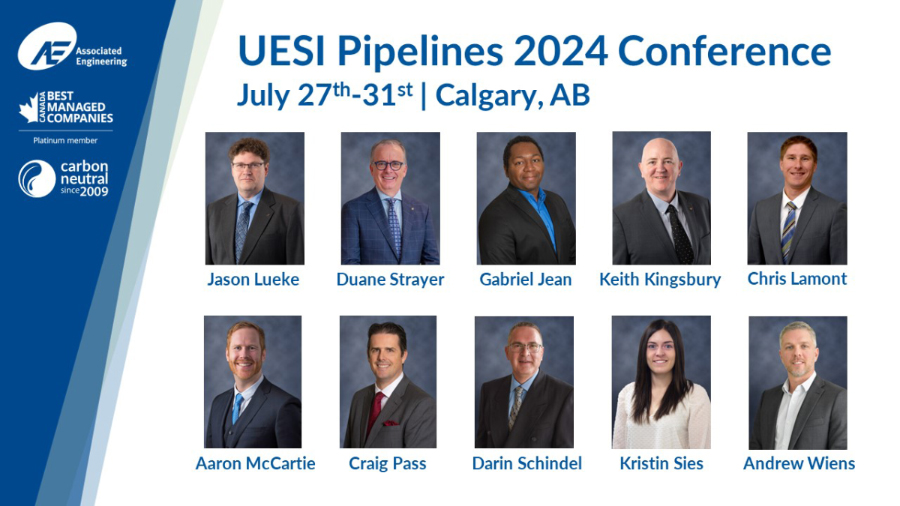
We’re excited to be part of the UESI Pipelines 2024 Conference in Calgary, AB this week! From serving on the conference organizing committee, moderating sessions, authoring papers, and delivering presentations in the technical track program, our participating staff have been busy in the lead up and expect a wonderful few days ahead!
Monday, July 29, 2024
2:00PM – 2:30PM | Macleod D Room
Valley Line West LRT – Drainage Relocation – Microtunnelling Construction Design and Impact
Chris Lamont
Design and construction on the new Valley Line West which connects downtown to the west side of Edmonton is currently underway. EPCOR owns and operates a number of sanitary sewers along the new LRT alignment. Due to the depth, length, and other utility conflicts, the primary sewer was designed to be replaced by primarily by microtunnelling methods. Shanghai Construction Group was awarded the project and began planning for several microtunnel drives. Due to the tight construction timeline two drives were planned to occur simultaneously by microtunnelling from both sides of an existing 1500mm diameter trunk at installation lengths between 400m and 980m. The anticipated jacking loads for the installations were identified as a concern as the existing deep trunk was not designed to take the laterally imposed 500 and 800 Tonnes cyclically over 200 times and at nonconcentric elevations. A finite element analysis of the proposed shaft design system and the loading imposed by the microtunnelling was completed to determine if the potential impacts to the existing tunnel were in excess of what could be resisted. This paper will discuss the steps taken to assess the structural impact of the construction loads on the existing deep sewer trunk. It will also go through the complications and issues encountered during construction and how they were mitigated through working with the owner to minimize public impact on such a large project.
2:30PM – 3:00PM | Glen 208-209 Room
NWIC Upper Plateau Separation Project: Reducing Flood Risk Through Innovative Storm Catchment Separation
Craig Pass, Andrew Wiens
The community of Sunnyside, North of downtown Calgary, Alberta, is located in the Bow River floodplain. Sunnyside is located below a 30 metre high escarpment which separates it from an upper plateau. 290 ha of this upper plateau catchment drains into storm trunks that connect to Sunnyside’s storm system and discharge to the Bow River. In 2013, Sunnyside was subjected to significant flooding twice over the span of two weeks. Associated Engineering worked with The City of Calgary to identify solutions to manage the upper plateau stormwater and reduce flood risk in Sunnyside. The design criteria required management of a 1:50 year rainfall event with a low Bow River level and a 1:5 year rainfall event when the river level is at a 1:100 year level. Associated assessed options to store and pump the stormwater. Feasible storage locations proved difficult to find in the developed, inner-city and pumping the flow proved costly, so Associated also examined conveyance options. Due to the estimated capital cost, the options were vetted through a Value Engineering session convened by The City. The recommended option which was advanced to construction proposed intercepting the upper plateau stormwater and conveying it to the Bow River via a 775 m long, 3.4 m diameter gravity storm trunk. The trunk, which includes a depressed siphon, will convey 20 m3/s during a low river condition and 11 m3/s to a high river. A portion of the trunk was installed by microtunnelling and was the largest diameter microtunnelling installation in Canada as of the installation date. By installing the trunk, the storm flows from the upper plateau catchment north of Sunnyside were separated from the local flows generated from within the community for discharge directly to the Bow River during low and high river levels. This created additional capacity in the local existing system, significantly reducing the flood risk for Sunnyside and adjacent communities. The paper and technical presentation will provide insight into the project planning, design and construction delivery.
5:00PM – 5:30PM | Macleod C Room
Saunderson Waterline – Large Diameter HDD Installation
Chris Lamont, Jason Lueke
The Saunderson PRV project is a multi-year project to upgrade water supply for the Lower Townsite (LTS) neighbourhood in Fort McMurray, Alberta. The project includes the construction of a new PRV chamber in the LTS, extension of the existing primary high pressure water supply line, and the installation of a new supply line from the new LTS PRV chamber to the existing Abasand Heights neighbourhood reservoir to by horizontal directional drilling (HDD). The focus of this paper is on the design and installation of the 450 m long, 914 mm diameter HDPE DR9 directionally drilled supply line crossing of Highway 63 from the LTS to the Abasand Heights plateau, a topographic elevation difference of approximately 65 m between entry and exit. Detail design of the installation included consideration of the complex geotechnical stratigraphy, elevation difference, short alignment, connection requirements and its setback from the plateaus top of bank, slope failure zone, and extremely tight workspace restrictions. Construction of the trenchless crossing installation was successfully completed in April 2023. Project complexities were anticipated during design and managed during installation as a result of the elevation difference between drill entry and exit including contingency measures to manage flush-backs during reaming passes, overbreak pipe support at drill exit for pullback, buoyancy control requirements during pullback, and annular space grouting post-installation. This paper will review the steps taken during design and construction to support the successful installation and review lessons learned through the process.
Wednesday, July 31, 2024
10:30AM – 11:00AM | Glen 208-209 Room
The City of Edmonton’s Sustainable Utility – Blatchford District Energy System
Aaron McCartie
Following the closure of the Edmonton City Centre Airport, the City of Edmonton has approved a redevelopment plan for the 536-acre parcel of land. The City’s Vision is that “Blatchford will be home to up to 30,000 Edmontonians living, working and learning in a sustainable community that uses 100 percent renewable energy, is carbon neutral, significantly reduces its ecological footprint, and empowers residents to pursue a range of sustainable lifestyle choices.” The overall District Energy System design utilizes inter-connected nodes of centralized heat pumps distributing ambient-temperature water to heat pumps in each building. This allows for sharing between buildings and flexibility for connection of additional energy sources in a staged build-out over time. Geoexchange, sewer heat exchange, auxiliary boilers and cooling-towers, Solar PV as a low-GHG electricity source, are included in the overall design concept. Combining the benefits of building energy efficiency, energy sharing within the system, and highly efficient heat pumps, results in greenhouse gas reductions at 75% below that of business as usual. The 3 MW Energy Centre for Phase 1 was commissioned in Q4 2019 with an initial 1 MW of HP capacity, and a 570 borehole geoexchange field under the future storm water retention pond as it’s renewable energy source. More than 1 km of large-diameter HDPE DPS has a planned 57 service connections. The City of Edmonton has established the Blatchford Renewable Energy Utility to own and operate the system. Blatchford has been recognized locally, nationally, and internationally, with awards including those from: Association of Consulting Engineering Companies – Canada; Canadian Home Builders’ Association; Consulting Engineers of Alberta; Federation of Canadian Municipalities; and most recently International Federation of Consulting Engineers (FIDIC). This presentation will discuss the assessment, design, and implementation of this innovative and forward-thinking utility project that provides low-carbon heating and cooling service to an urban in-fill, master-planned, sustainable community.
10:30AM – 11:00AM | Telus 104-106 Room
Buffalo Pound Non Potable Water Supply System – Regina Regional Pipeline
Darin Schindel, Keith Kingsbury, Kristin Sies
The Buffalo Pound Non Potable Water Supply System (BPNPWSS)– Regina Regional system will supply non-potable water from Buffalo Pound Lake to industrial customers in the southwest and northeast regions around Regina. The Regina Regional System is an extension of the existing BPNPWSS – East which consists of a lake intake, pumping station and pipelines that currently supply non-potable water to industrial customers in the Belle Plaine corridor. The project as a whole includes two booster pump stations, 65 kilometers of pipe and service laterals and metering stations at various customer sites. The planning of the pipeline began with utilizing GIS to show existing utilities, route challenges and initial consultation with stakeholders. Once the route was chosen, hydraulic analysis was completed to determine the required pressure rating and diameter of the pipe to deliver the required water to the end users. The results of that analysis were that the pipeline would be broken down into 3 sections: Section 1 being 34.5 kilometers of 600mm with an operating pressure of 275psi, Section 2 being 24 kilometers of 500 mm with an operating pressure of 250psi, and Section 3 being 5.5 kilometers of 400mm with an operating pressure of 150psi. The design of the pipeline took a unique and alternative delivery approach. The focus from the client, Saskatchewan Water Corporation (SaskWater), was to determine through industry consultation the most cost effective pipeline material for each section and to determine if the contractors chosen had experience in installing the chosen pipe type. Ductile iron, steel, and HDPE were candidates for Sections 1 and 2, with PVC added as an option for Section 3. The design of the pipeline was completed to 70%, without a specified pipe type for procurement. A Request for Supplier Qualifications (RFSQ) pre-qualified 3 contractors to submit a proposal to complete the work. The proposals included the Contractor’s proposed pipeline material for each section meeting the specified criteria, work plan and schedule, additional details on their previous experience and their proposal price. Once the pipe types were chosen, the design was completed with the selected Contractor’s input and construction began in May 2023. This paper will provide an overview of the planning and design process determining the pipeline route utilizing GIS, to 70% design of the pipeline, and finally to obtaining a qualified contractor and completing the design. We will also discuss the challenges and benefits that this approach brought on.
Siksika Nation develops strategic approach to improve condition of housing supply
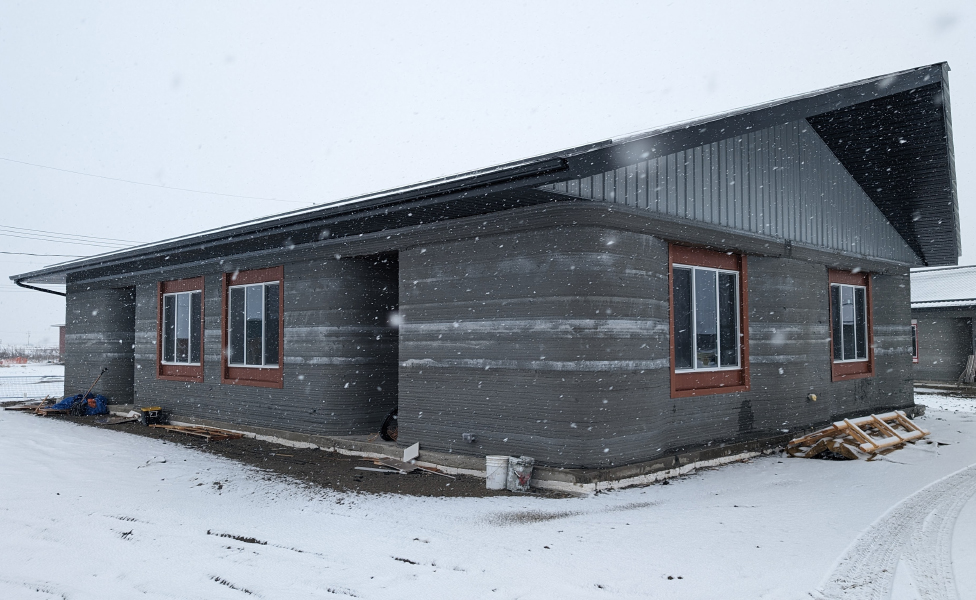
Located 95 kilometres east of Calgary, Siksika Nation is growing quickly, and there is a shortage of safe and quality housing. Existing homes require significant work to bring them up to living standard, and more homes need to be built to accommodate the growing population. Many Elders and residents live in homes requiring repairs or renovations to address safety and health concerns.
The community prioritized Elders’ units and multi-generational homes in which Elders reside for the pilot project. Elders represent the most vulnerable members of the community. Focusing on Elders’ needs first improves safety and well-being for Elders and respects Elders who play a key role in Indigenous Communities, passing on their knowledge and cultural principles.
The Nation needed to identify what work needed to be done, create a strategy (with limited funds and need for transparency) to conduct the required maintenance, and manage the ongoing repairs.
The Siksika Nation Housing Department provides and maintains the Nation’s public housing for approximately 1,235 homes. In 2022, the Housing Department completed over 200 inspections of Elders’ homes with the help of home inspection firms, whose comprehensive reports detailed recommendations for repairs.
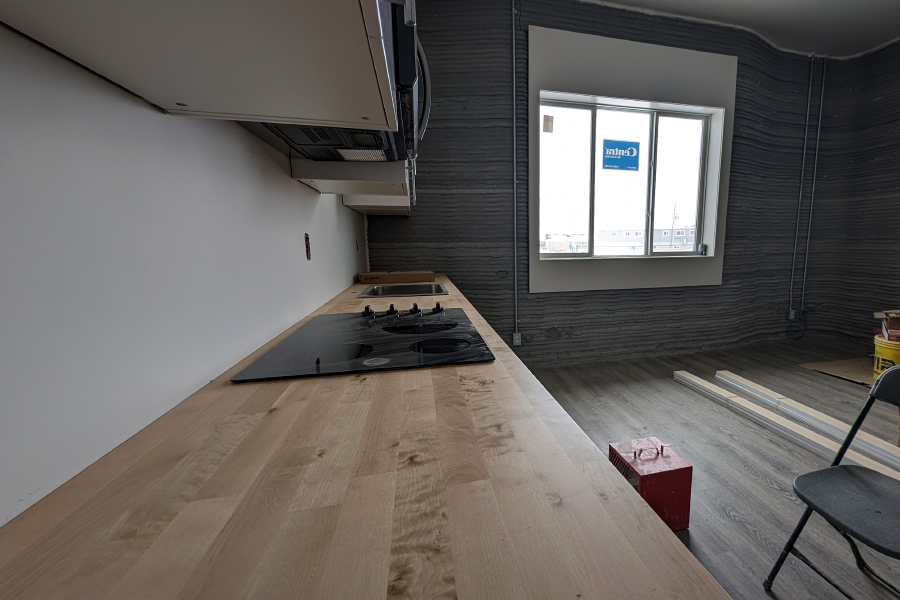
The Housing Department has limited funding and labour resources to meet the community’s needs, and also faces capacity constraints. The Department engaged Associated Engineering to assist with developing an efficient and cost-effective action plan, and provide project management support for the first phase of the Elders’ Homes Repair Program. In addition to assisting with the repair program, we helped the Housing Department with strategic planning, and developed tools to help build internal capacity to plan and budget future work.
Project Manager, Abu Waraich, tells us, “Our work included a significant data management component. The home inspection reports contained a large amount of information in text form. Converting this text to a useable form required creating programming scripts to extract and process over 5,000 recommendations from the inspection reports.”
The home inspection reports were completed almost two years ago. The reports assigned priorities to all of the recommendations, so risks to the safety of the residents could be addressed first. However, since the inspections, some of the information in the reports were outdated, and in many cases the condition of different components became worse.
Abu says, “With digitization of the data in the reports, the priorities assigned to different repairs could be modified as new information became available, allowing the project team to quickly pivot and allocate funds within the project budget to the highest risk homes and items. Items which had lower risk to residents could be assigned lower urgency and can be addressed in future phases.”
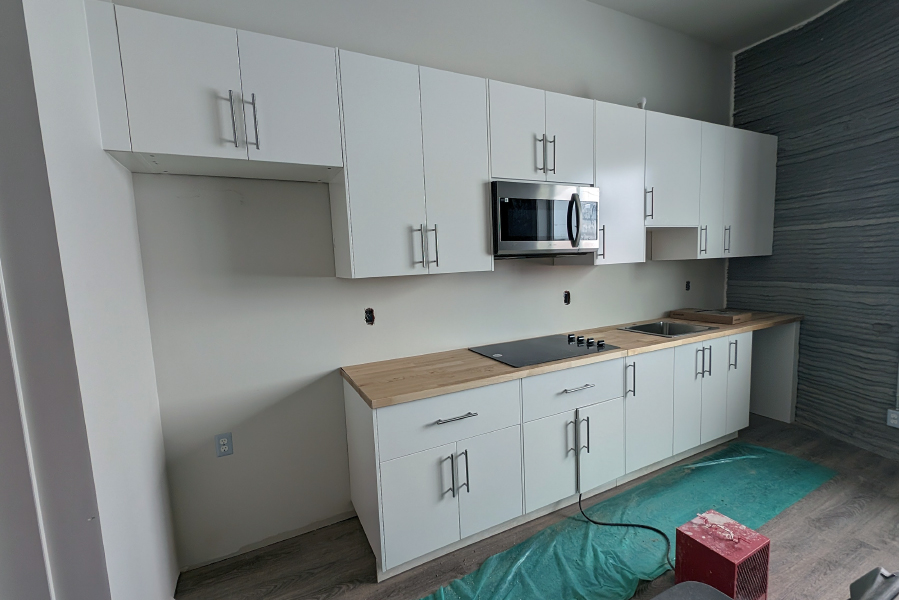
Our team worked closely with the Housing Department to ensure that they were involved in the development and rollout of plans and tools. When developing the costing spreadsheet to help operations staff estimate the cost of completing repairs and maintenance, Associated worked closely with Housing Department staff and a cost consultant so they could understand the new approach to costing and incorporated their feedback to make the tool as user friendly as possible.
During the repairs and renovations, Associated kept residents informed about the repair work. Project team member, Jorey Robin, says, “We worked hard to establish a rapport with residents. Along with the contractor and the Siksika Housing Department, we met with Elders to describe the work being completed on their homes and explained the phased approach.”
Associated is currently reviewing and organizing the various Housing Capital Programs and identifying where the Nation could improve their data management so that they can improve how they manage projects and funding/grant applications.
Our key personnel on the project are Abu Waraich, Jorey Robin, and Craig MacDonald.
Associated Engineering welcomes Chad Maki as General Manager of our Alberta North operation
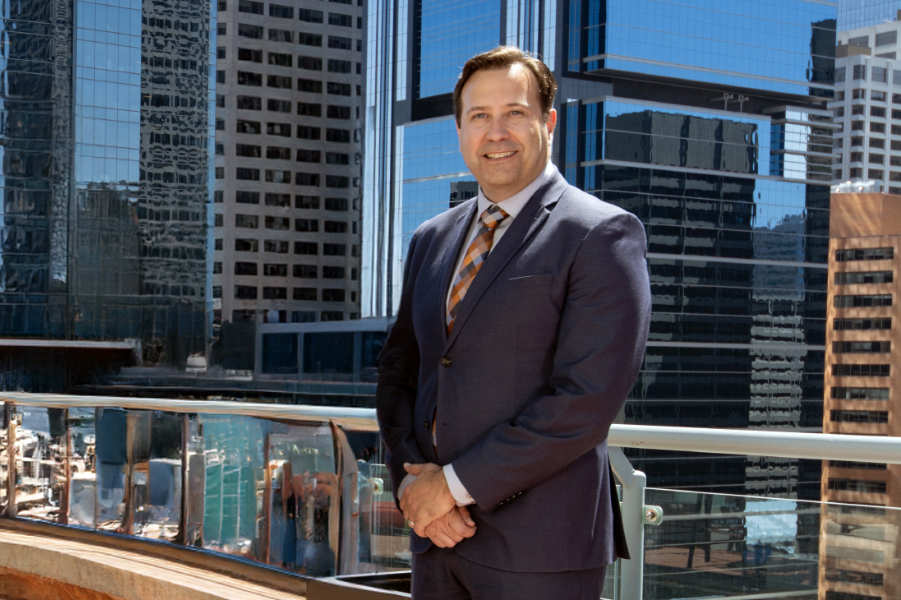
Associated Engineering is pleased to announce Chad Maki, P.Eng., as the new General Manager of the Alberta North operation, effective July 1, 2024. Chad succeeds Helder Afonso as General Manager, who is retiring after 37 years of service with the company.
Chad began his career at Associated Engineering as a summer student. After earning a bachelor’s degree in civil engineering, Chad joined Associated Engineering in 2001, and subsequently progressed in roles from design engineer to project manager, group manager, division manager, and now General Manager. An accomplished engineer and leader, Chad has 23 years of experience on water/wastewater, solid waste, and road infrastructure, as well as urban and industrial developments across Alberta, including award-winning projects for Athabasca County and the City of Edmonton. He brings strong technical abilities and a proven track record of leading teams and successfully delivering projects to his new role as General Manager.
On his appointment, Chad says, “I’m honoured and excited to take on this leadership role with our Alberta North operation and to work with our talented team. I look forward to collaborating with our clients as their trusted advisors to help build more sustainable and resilient communities.” Chad adds, “I want to thank Helder for his support and guidance over the years and through this leadership transition.”
“Chad is an inspiring leader who promotes diversity and staff development,” said Helder Afonso, retiring Vice President and General Manager, Alberta North. “With his strong business development skills, business acumen, and vision, Associated Engineering will continue to flourish.”
Associated Engineering congratulates Chad on his new role, and thanks Helder for his many years of dedicated service and wishes him a long and healthy retirement!
Emergency dredging of the Hay River aids in maintaining key marine operations and critical resupply link
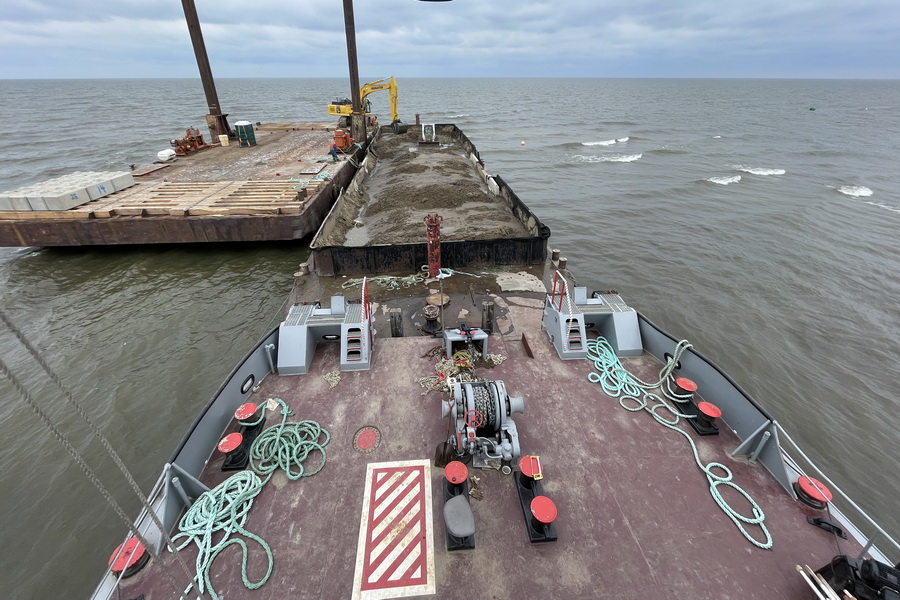
The Hay River Harbour is the primary operational base for Marine Transportation Services (MTS), a marine shipping service operated by the Government of the Northwest Territories. As the key hub for rail, highway, and marine networks serving 12 communities, MTS provides marine resupply services for transporting petroleum products and other bulk freight.
Bulk resupply, particularly of fuel, is a complex and multimodal network across the Northwest Territories. Each community’s resupply profile is unique and is influenced by a combination of storage infrastructure capacity, duration and timing of road access, marine river or ocean access, lateral staging options, and other supply-chain factors. Marine resupply forms a critical component of bulk resupply. Alternative options require significant lead time and contingency options are logistically and cost prohibitive.
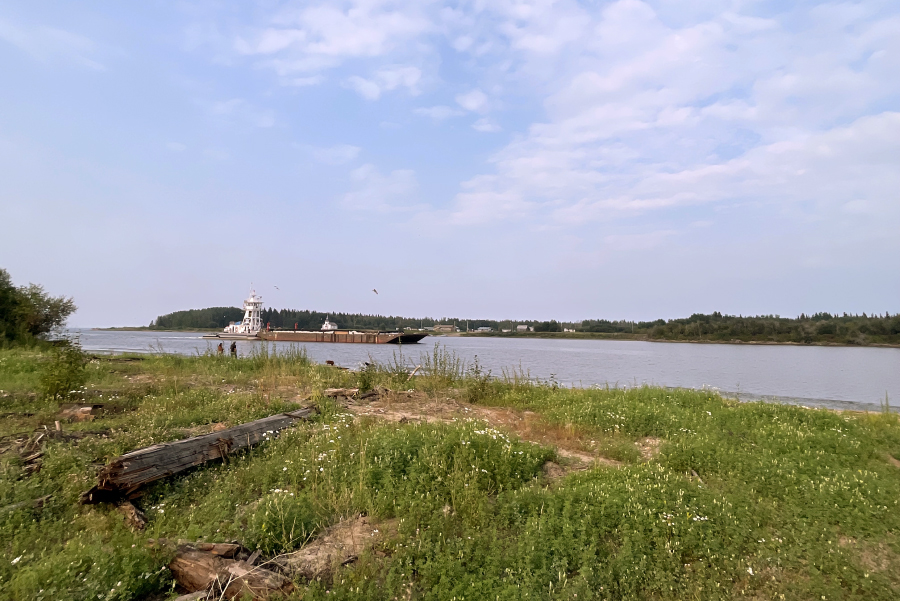
The harbour was last significantly dredged in 1997. Since then, the buildup of sediment in the harbour has created navigation hazards for marine vessels and now threatens this important marine supply-chain hub. The harbour required restoration to maintain the viability of key marine operations for both government and industry.
Project Manager, Rebekka Lindskoog, says, “The current bathymetry and water elevation data suggest that insufficient depth will threaten resupply operations. Restoration is critical to protecting public safety and infrastructure to restoring a safe and reliable resupply route.”
In 2022, the Town of Hay River flooded during spring break-up. This event likely contributed high amounts of sediment into the river. As the summer progressed, the water levels began to drop at an abnormal rate. By the early fall, vessels were being grounded on the shoals, particularly at the outfall into Great Slave Lake.
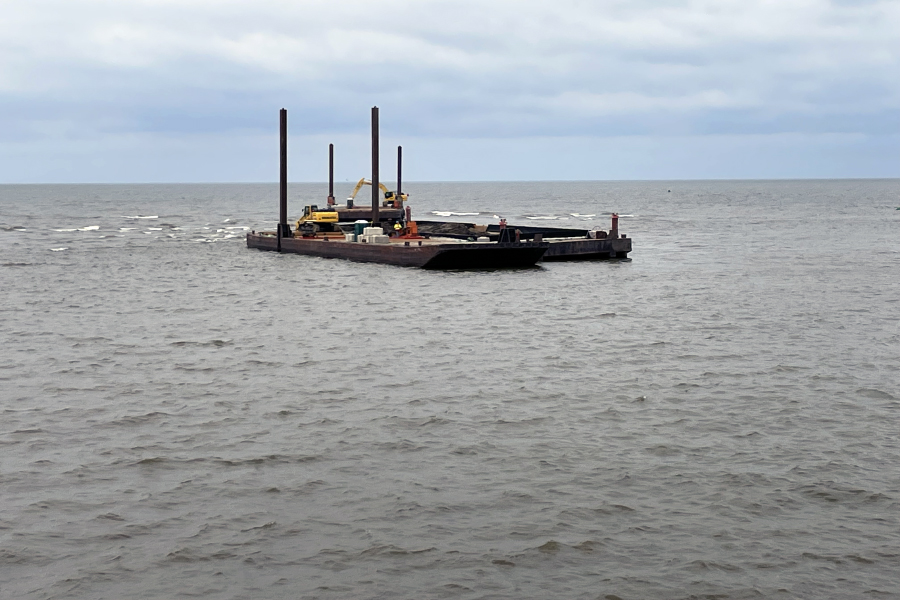
On behalf of the Government of the Northwest Territories, Department of Infrastructure, Westmar Advisors retained Associated for the environmental and regulatory leadership for the emergency dredging program. The contractor for the dredging program is locally owned Rowes Construction.
Rebekka tells us, “We focused on developing a way to restore navigability in the channel, recognizing the extreme constraints posed by the compressed timing to satisfy regulatory and procurement requirements.” The technical design established a channel width and depth that would provide minimum passage requirements of the largest draft vessel and a width that would facilitate a single-barge, wide configuration for MTS, with a safety buffer.
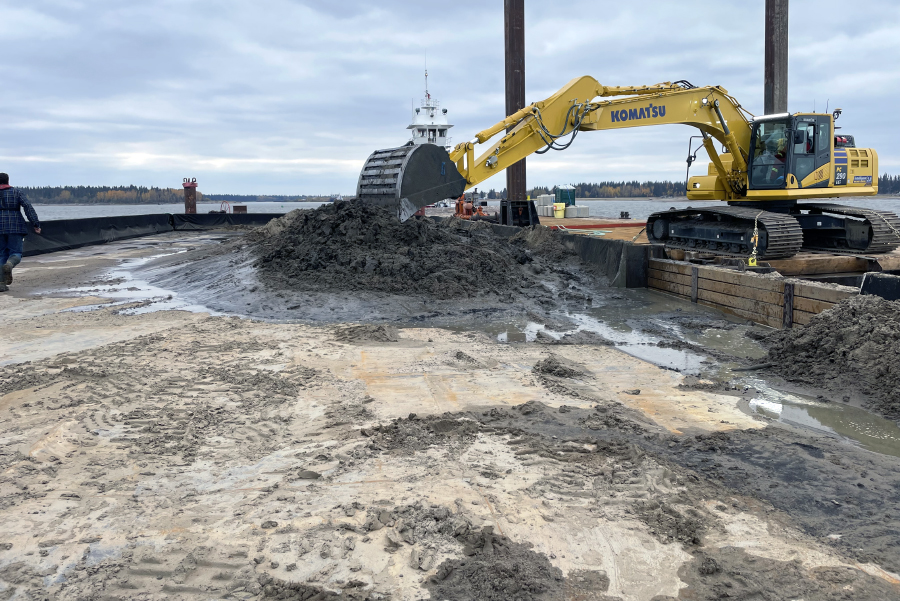
The project involved mechanically dredging sediment from two areas in the Hay River to open an emergency marine navigation channel 30 metres wide and 2.4 metres deep.
The team received the required regulatory approvals under the emergency provision, in time for the dredging program to be conducted during the least-risk fish window.
“Two days after we began dredging, the Town of Hay River had to be evacuated due to wildfire.”
In 2023, approximately 5,600 cubic metres of sediment was dredged and about 78,000 cubic metres remains to be removed in 2024.
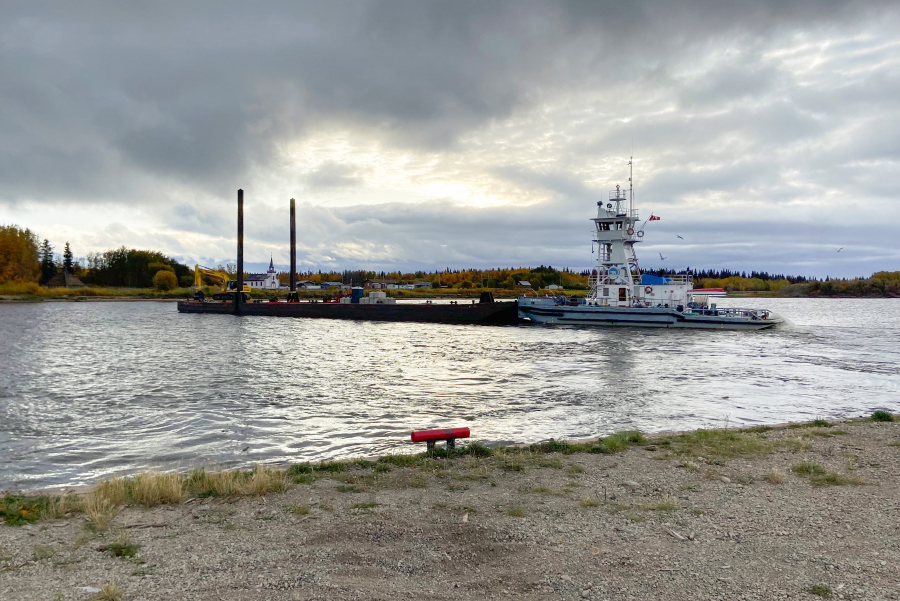
“We have updated and maintained the regulatory approvals for the second year of dredging, including permission from Fisheries and Oceans Canada for an extended window, as a result of community engagement feedback and support for the program.”
The remainder of the emergency dredging program is currently underway and will include working alongside with Indigenous auditors from the local Indigenous communities.
Parallel to the emergency program, Associated is leading a multi-disciplinary feasibility analysis for the Hay River long-term dredging program.
Associated’s key personnel on the project are Rebekka Lindskoog, Candace Bryks, Cassio Ishii, Brett Elmslie, Dean Foster, Tyler Mehler, Ryley Corcoran, and Brian MacGillivray.
Melville Water Supply System provides resilient, reliable, and cost-efficient drinking water to the city
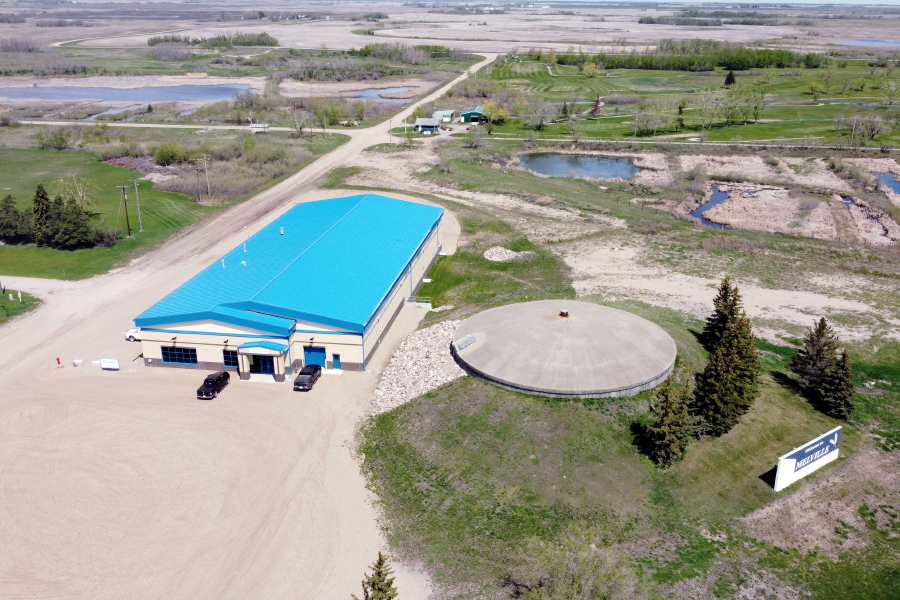
Since its founding in 1908, the City of Melville in east-central Saskatchewan has endured challenges providing reliable, quality drinking water to residents. Melville’s surface water supply was difficult to treat and the area is prone to droughts. As a result, the City added a supplemental groundwater supply in 1989.
The City implemented Canada’s first electrodialysis reversal (EDR) process to treat its highly mineralized groundwater supply. In 2016, with this equipment near the end of its service life, SaskWater, the plant’s owner/operator, retained Associated Engineering to design and oversee construction of a new water treatment plant using only groundwater.
Project Manager, Peter Hooge, says, “Associated Engineering shared SaskWater’s and Melville’s strategy and vision to use the reverse osmosis (RO) process to treat the groundwater supply for the City. Once completed, this facility would be one of the largest, municipal reverse osmosis water treatment plants in the province.”
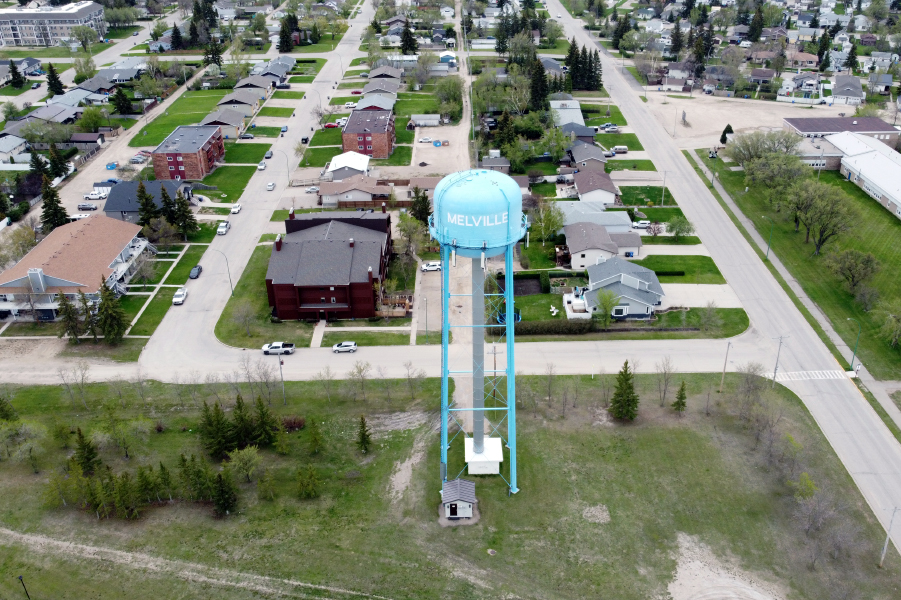
Associated advocated for the addition of pre-treatment upstream and post-treatment downstream of the RO, which would increase the RO membrane service life, reducing operating and maintenance costs and minimizing RO wastewater volumes generated.
SaskWater, Associated Engineering, and Beckie Hydrogeologists (BHL) collaborated on the design of the new wells, supply pipeline, and solar panel installation, which interfaced with Associated’s design of wellfield pumping infrastructure. Associated’s multi-discipline team included civil, structural, mechanical, electrical, instrumentation and controls designers.
A complete SCADA (Supervisory Control and Data Acquisition) system was also part of Associated’s design, which interfaced with all components of Melville’s Potable Water Supply System. The project also included demolition of the old plant and the deep well injection system formerly used for EDR process wastewater disposal, and decommissioning of the surface water supply.
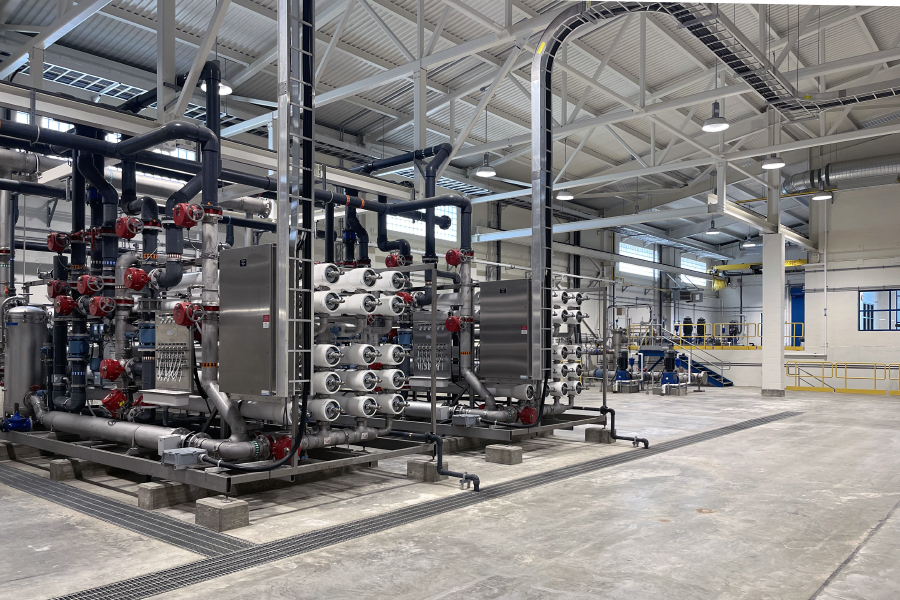
Project Engineer, Shengtao Weng, says, “We designed a tailored pre-treatment system, including oxidation, detention, and gravity filtration for removal of iron, manganese, and arsenic.” The post-treatment system encompassed pH correction and saturation index adjustment (control water’s corrosivity).
The new Melville Potable Water Supply System includes two new groundwater supply wells in the Hatfield Aquifer, located 30 kilometres south of the plant, a new raw water transmission line from the Hatfield Aquifer wellfield, re-use of two existing groundwater supply wells in the nearby Melville Aquifer and the associated raw water transmission line, a new water treatment plant in Melville, re-use of an existing 4550 cubic metre gunite reservoir, repurposing existing wastewater ponds, and potable water connections to the City distribution system and water tower.
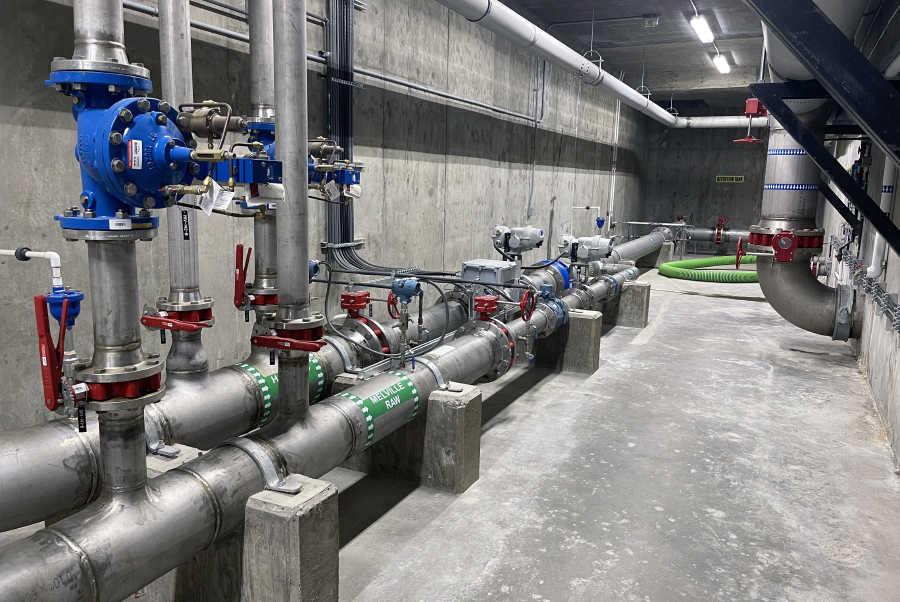
Associated Engineering’s design allowed construction and commissioning to proceed without unplanned water supply service disruptions, while fully integrating existing non-plant infrastructure, where possible. Initially located adjacent to the old facility, the new plant design facilitated raw water and treated water piping interconnections, including a challenging connection into the existing gunite reservoir.
Peter tells us, “The new process incorporates wastewater retention and release, reducing environmental impact and greenhouse gas emissions from the former deep well injection system.”
Melville now has the highest consistent quality drinking water in its 115 year history
The complete system, including the new 30 kilometre raw water supply pipeline, was successfully commissioned in March 2022. Operating costs are 20-25% lower than the old plant and maintenance costs are significantly lower.
Delivered on time and under budget, the water treatment plant provides Melville residents with affordable, high quality, sustainable, and reliable drinking water that supports growth, economic development, and quality of life.
CUIIC awarded major NSERC Alliance Grant for underground infrastructure research
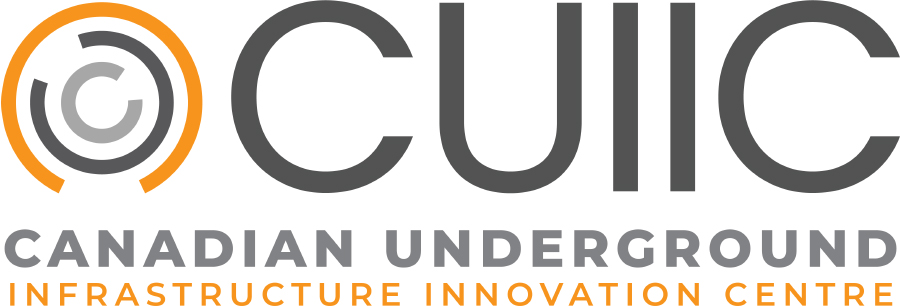
The Canadian Underground Infrastructure Innovation Centre (CUIIC) announces the award of a Natural Science and Engineering Research Council (NSERC) Alliance Grant for the groundbreaking project titled “Greenhouse Gas Emission Reduction in Design, Construction, Repair, and Maintenance of Underground Infrastructure.”
This initiative, led by Dr. Alireza Bayat, Professor of Civil and Environmental Engineering and Director of CUIIC, brings together three Canadian universities to develop innovative strategies and technologies aimed at mitigating greenhouse gas emissions across various phases of underground infrastructure projects. The co-applicants include Dr. E. Davies, Dr. L. Hashemian, and Dr. S. J. Birchall (University of Alberta); Dr. R. Dziedzic (Concordia University); and Dr. I. L. Stefanovic (University of Toronto).
NSERC and 21 industry partners are funding cash and in-kind contributions totalling three million dollars over five years. The research will provide training opportunities for ten graduate and undergraduate students, allowing them to gain hands-on experience and interact with industry professionals in the field of underground infrastructure.
The Industry Partners include: Associated Engineering, EPCOR Water Services Inc., Metro Vancouver, Insituform Technologies, Region of Peel, AECOM, UDI Edmonton, Alberta Roadbuilders & Heavy Construction Association, Mott MacDonald Canada Ltd, Stantec Consulting Ltd., ATCO Gas and Pipelines Ltd, Dura-Line, eTrenchless Group, Lafarge Canada Inc., North American Society for Trenchless Technologies-NW Chapter, ParklandGEO, Precon, PW Trenchless Construction Inc., Westlake Pipe & Fittings, Benjamin Media Inc., Uni-Bell PVC Pipe Association.
Jason Lueke, P.Eng., Ph.D., National Discipline Leader, Trenchless Technologies, says, “Associated Engineering is excited to collaborate with CUIIC, NSERC, and our industry partners on this important program to develop strategies to reduce GHG emissions on underground infrastructure projects.”
CUIIC, housed at the University of Alberta, continues to be at the forefront of research and innovation in underground infrastructure leading collaborative efforts between academia and industry to address critical infrastructure challenges.
Dr. Bayat expressed his excitement about the project, stating, “This initiative will advance sustainable practices in the design, construction, repair, and maintenance of underground infrastructure, significantly reducing greenhouse gas emissions and contributing to environmental conservation efforts.”
Collaborating with Lake Babine Nation identifies unique requirements for new cultural gathering centres
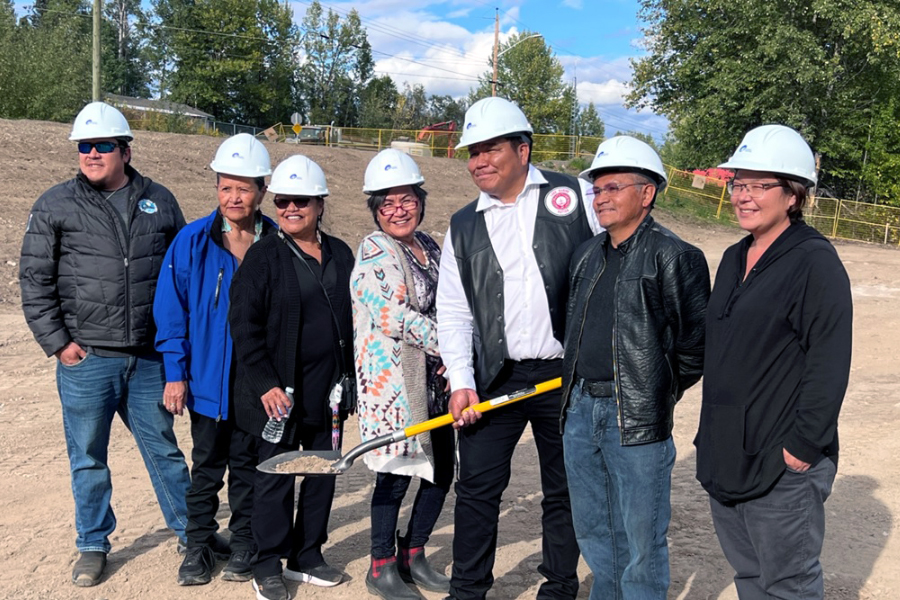
Since 2022, Associated has been working on the design of Cultural Gathering Centres at Tachet and Wit’at for the Lake Babine Nation in BC.
Freda Leong, Associated’s National Leader, Indigenous Communities, tells us, “We are proud of the positive relationships we have built with the Nation and involving their steering committees and community members in every step of the design of two Cultural Gathering Centres. They have guided us through the design of these spaces which will support the communities. The designs are not twins, but are cousins. They are braided in intention, but include unique and special features – just like the people and the communities of Tachet and Wit’at.”
In 1876, the Federal government enacted the Indian Act, which gives the government the power to manage the affairs of Indigenous Communities and Peoples. The Federal government believed that Indigenous ceremonies like the potlatch prevented the assimilation/integration of Indigenous Peoples, and subsequently instituted an amendment to the Indian Act that banned the potlatch from 1884 to 1951. The loss of ceremony was crippling to Indigenous Peoples, as these ceremonies are deeply tied to their history, language, culture, community, and values.
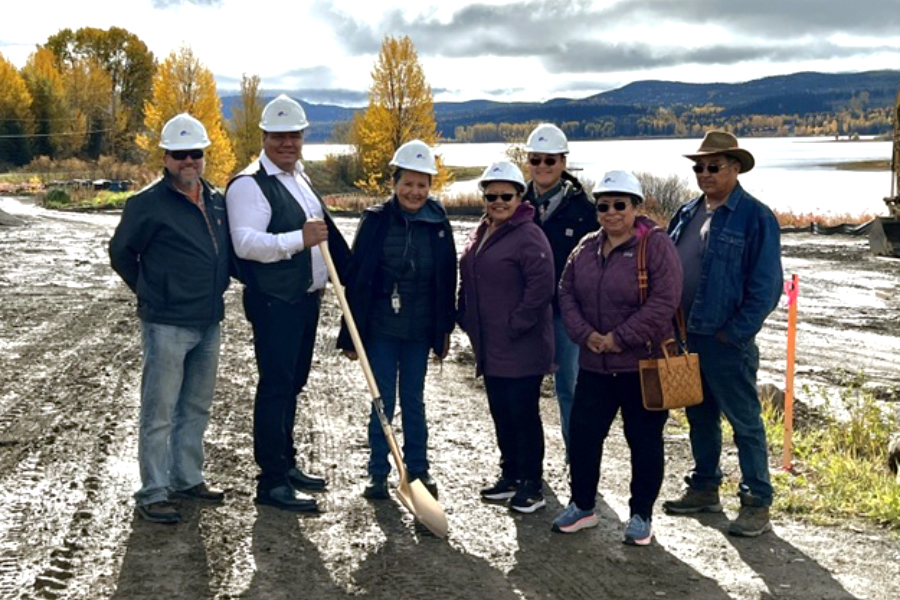
Freda says, “During a visit to Woyenne, as part of our work on their Capital Asset Needs Assessments, conducted under First Nations Child and Family Services for Lake Babine Nation, we conducted a survey of the local Child and Family Services team and community members. Their responses will help determine the capital asset investments required to support child and family services through a prevention lens. What we heard from community members and Elders during our survey is that there is a need to bring back ceremony, culture, and language; to reconnect to the land, community, and spirit; and to heal through reconnection.”
While in Skidegate, Associated’s team met with the Skidegate Haida Immersion Program (SHIP) and attended an Open House to reach out to Elders and community members to gather their input and knowledge for the Child and Family Services Capital Asset Needs Assessment. One Elder told our team that their strength and sense of self was lost through colonization. Some spoke about the shame and fear of speaking their language when they were young and the punishment for practicing their culture, and how it was forced out of their lives. Elders spoke of the their healing through language and culture, and how they are regaining their strength.
Freda says, “Through wonderful programs such as SHIP, Elders are reconnecting, gathering strength, and passing on their culture, language, and ceremony to community. Today, we see the celebration of language and culture. Language and culture are healing. Gathering is healing. The new Cultural Gathering Centres for these communities will support and advance healing.”
Modernizing City Hall’s mechanical systems improves operational efficiency and helps Brampton to meet compliance requirements
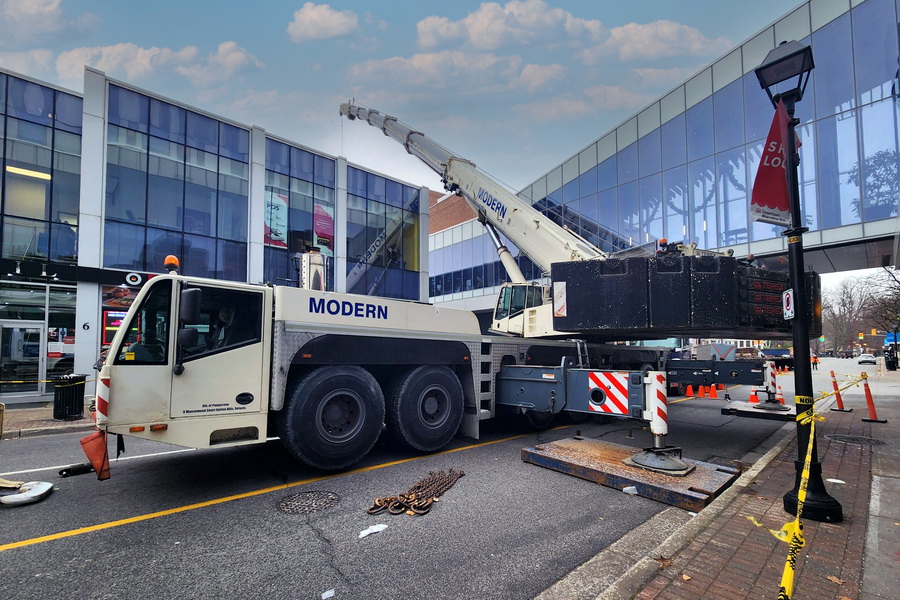
Brampton, Ontario’s City Hall is a vital hub for municipal operations and hosts numerous events, council meetings, and administrative activities. As part of an ongoing commitment to replace aging infrastructure and ensure operational reliability, the City of Brampton engaged Associated Engineering to undertake critical upgrades to the emergency power system and existing air handling units (AHUs) as a part of the HVAC systems at City Hall. The project’s scope of work also included updating the cooling and humidification systems as part of the AHUs, replacing the humidifiers serving the AHUs, and upgrading five existing drinking fountains to comply with current accessibility requirements, codes, and standards.
The City of Brampton wished to improve the reliability and efficiency of the emergency power system and HVAC infrastructure. The outdated emergency diesel generator and AHUs posed significant issues, including potential operational disruptions during power outages and inefficiencies in maintaining indoor air quality and temperature. Project Manager and Building Mechanical Lead Engineer, Azad Khamforoush, advises, “We worked with the City to develop a robust solution to mitigate these issues, provide uninterrupted operation, and meet compliance standards.”
The project team overcame many challenges during design. These included a lack of background documentation and restricted access to the generator room due to existing, large, rooftop cooling towers blocking the only entry to the room; sequencing the construction work and managing a crowded City Hall with noise and odour restrictions during occupancy hours; supply-chain issues causing delays in generator delivery and challenging design constraints that limited acceptable generator vendors; complex lifting and rigging operations required for demolishing the old generator and transferring the new one to the highly restricted rooftop generator room; and coordination with neighbouring businesses for potential temporary power shutdowns during the crane lifting process.
“The design carefully considered sustainability by optimizing the generator and AHU systems for energy efficiency. The new systems are designed to reduce energy consumption and enhance reliability, contributing to the City’s long-term adaptability and sustainability goals.”
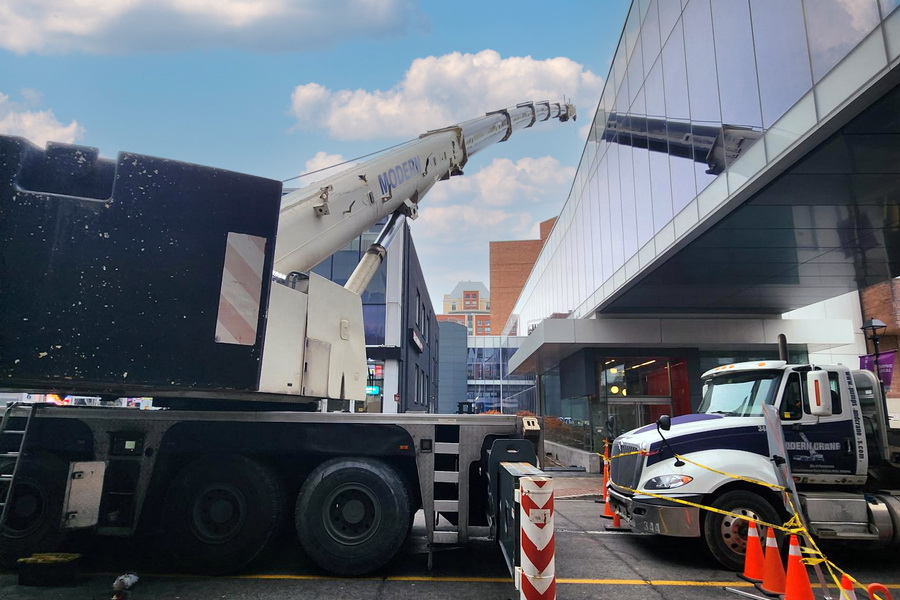
Azad tells us, “We came up with an effective solution to use an existing exhaust damper opening on the penthouse’s exterior wall for generator entry and exit, coordinated with vendors to ensure accurate dimensions of the new generator set, and collaborated with crane consultants to confirm the feasibility of the lifting operation in a constrained urban environment. We also requested hiring of specialized millwright teams along with a crane consultant in the design documents for safe generator demolition and installation. We phased the work to avoid operational disruptions. This required extensive planning to manage constraints of working in a busy, urban environment.”
The team implemented a phased approach for AHU replacements to ensure the continuous operation of HVAC systems at City Hall. To accommodate unforeseen supply-chain issues, timelines and budgets were adjusted. Meticulous planning and coordination helped to overcome changing circumstances during construction.
The project is nearing completion, with all equipment installed and mechanical items commissioned. The final commissioning of the generator set is pending, ensuring the City Hall will benefit from a reliable emergency power system and efficient HVAC operations.
The project highlights Associated’s capability to manage complex retrofit projects in challenging environments, leveraging our experience on municipal and industrial projects. Associated’s key personnel on this project are Azad Khamforoush, Dusan Fil, Yang An, David Holyer, and Dennis Cheng.
John Maree highlights the value of his mentors who influenced and guided his career journey
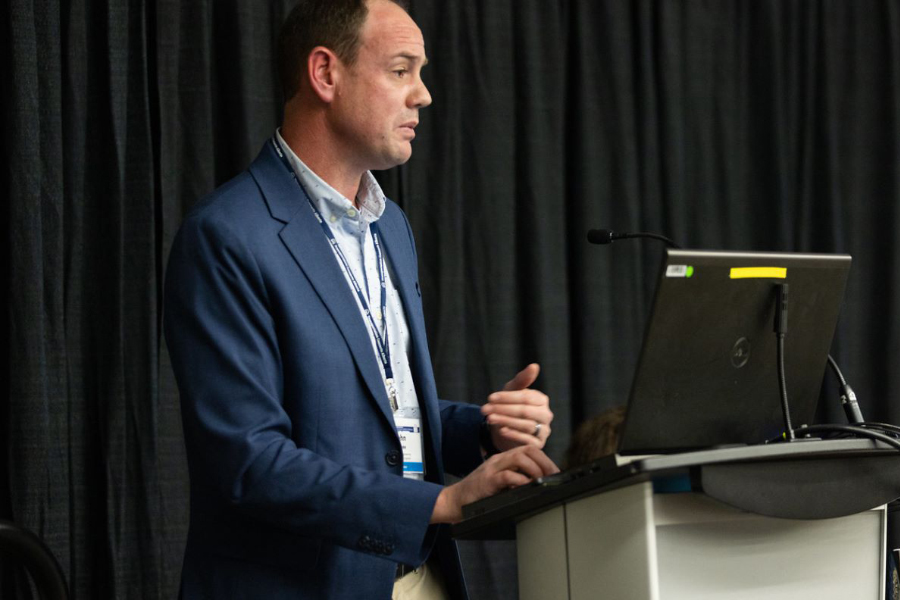
As a young child growing up in South Africa, John Maree was inspired by his father and fascinated by the work that he did and how he provided for his family as an engineer. John recalls, “I was also greatly influenced by my grade 12 math teacher. She believed in me and motivated me to such an extent that I still carry that motivation and gratitude with me today. She played a significant role in my success.”
John shares that an early mentor in his career taught him about self-confidence and instilled in him the value of his contributions to projects.
“He introduced me to and taught me pavement engineering, which sparked a passion for me; he was extremely motivating. To this day, we continue to be friends.”
In South Africa, John successfully progressed in his career and by his early-thirties, he had become a regional technical manager and later a technical director. Seeking a new challenge, John tells us that he applied for a role at Associated Engineering.
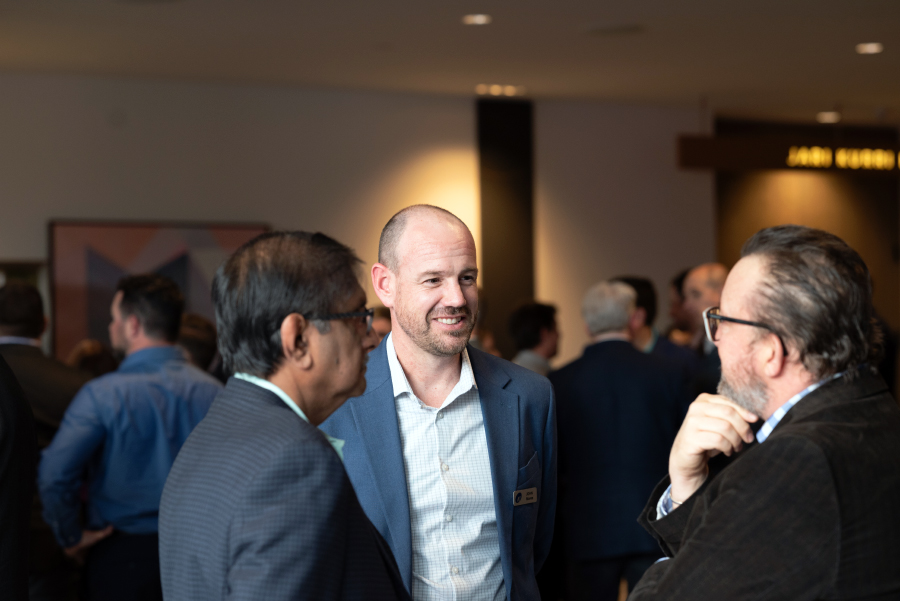
John says, “During my interview with Eben Kruger, he spoke highly of Associated Engineering. Eben’s passion for the company was truly evident. Now, after nearly five years with the company, I can confirm Eben didn’t exaggerate. I’m incredibly grateful to Eben and the company for giving me an opportunity. Recently, I was invited to become a shareholder of the company, which is something that I am very thankful for and proud of.”
A Senior Transportation Engineer in our Edmonton office, John specializes in the design of rural and urban roads in Northern Alberta. John tells us, “I truly love this work. Roads are the backbone of our society. I’m proud to contribute to building a better Canada.”
Since joining Associated in 2019, John has participated in many interesting and challenging projects, such as the Valley Line South LRT in Edmonton, North Corridor Improvements in St. Albert, and the twinning of Highway 63 in Northern Alberta.
“The North Corridor Improvement project is a highlight for me as it involved a comprehensive road redesign. The design included a new southbound alignment, while the northbound lanes underwent rehabilitation. The project addressed critical intersection connections and ensured efficient surface water drainage to designated low points. Additionally, it incorporated dedicated infrastructure for pedestrians and cyclists.”
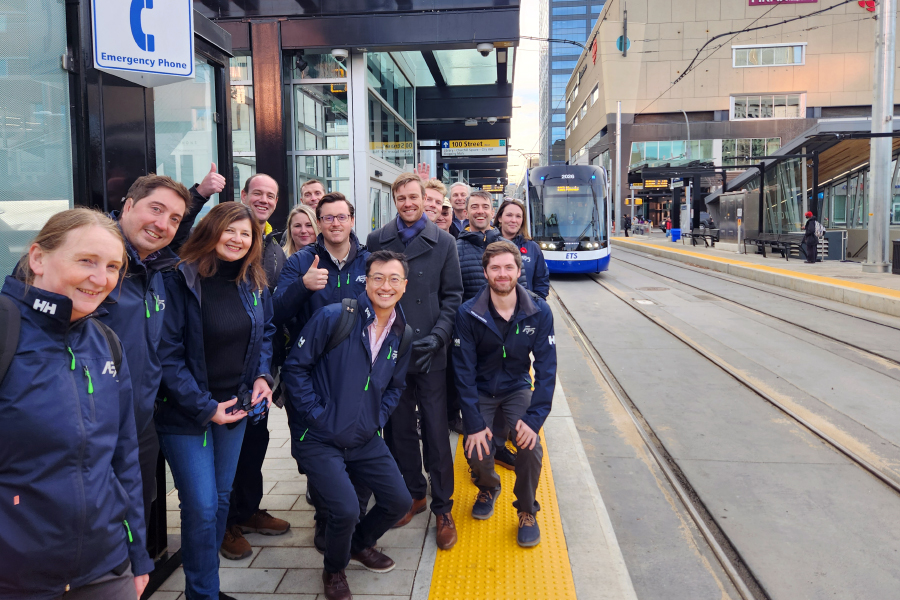
John tells us his experience at Associated Engineering has been very positive. He explains, “While it initially took some time to adjust to the different work environment in Canada, compared to South Africa, I truly appreciate the many extra activities and opportunities the company offers.” John shares that having worked for several companies before joining Associated Engineering, he can honestly say this is a great place to work.
When asked about his advice to young professionals, John recommends being open to opportunities. He advises, “Saying ‘no’ to certain tasks might close a door that could have been a very fulfilling opportunity, or at least a stepping stone to a satisfying career.”
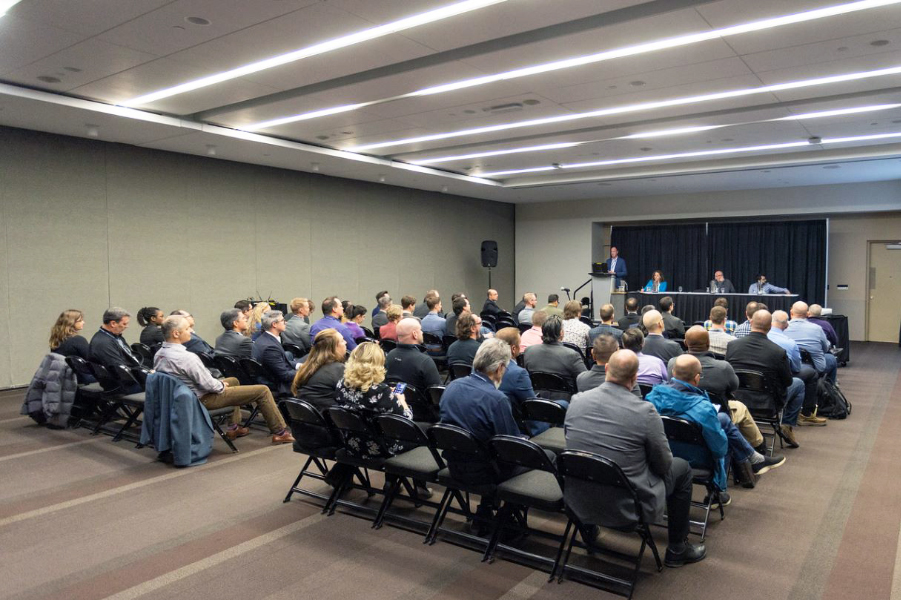
“I firmly believe in knowledge transfer. Whenever possible, I share my knowledge with our junior staff. I recognize that they are the future of this company, and that knowledge transfer benefits everyone, including myself, the individual receiving it, and ultimately, the company as a whole.”
Furthermore, John believes that nobody knows everything, so he always encourages his team to ask questions.
Professionally, John is currently the Secretary of the Transportation Association of Canada (TAC) Geometric Design committee, a member of the TAC roundabout design sub-committee, and a member of the Pavements committee. Within Associated Engineering, he is a member of the Roadways and Highways Discipline Interest Group.
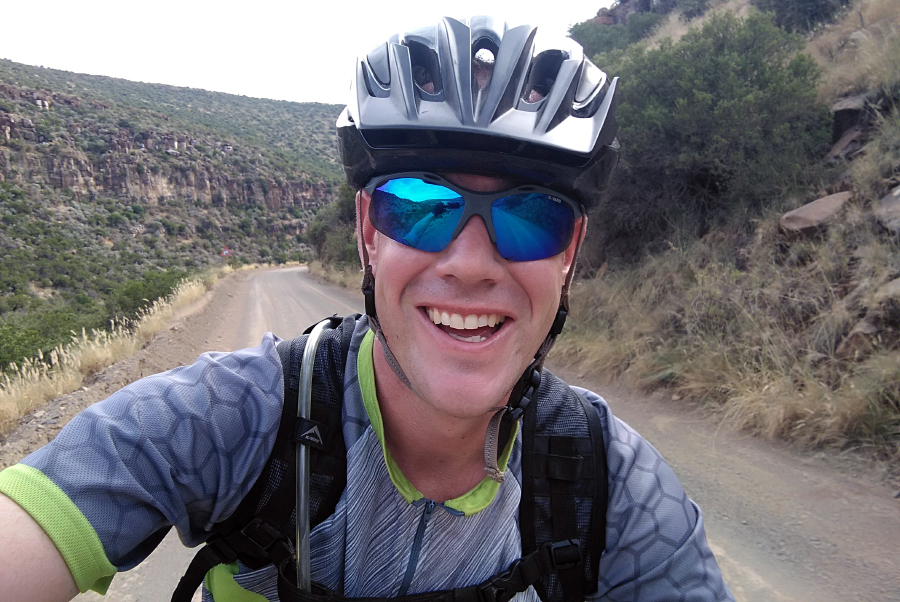
Outside of work, John enjoys spending time with his family and friends over a braai (South African barbecue). Recently, John has taken up skiing, and also enjoys running, mountain biking, and playing the electric guitar.
[ViewPoints] Bridge Management: Strategic approach delivers value
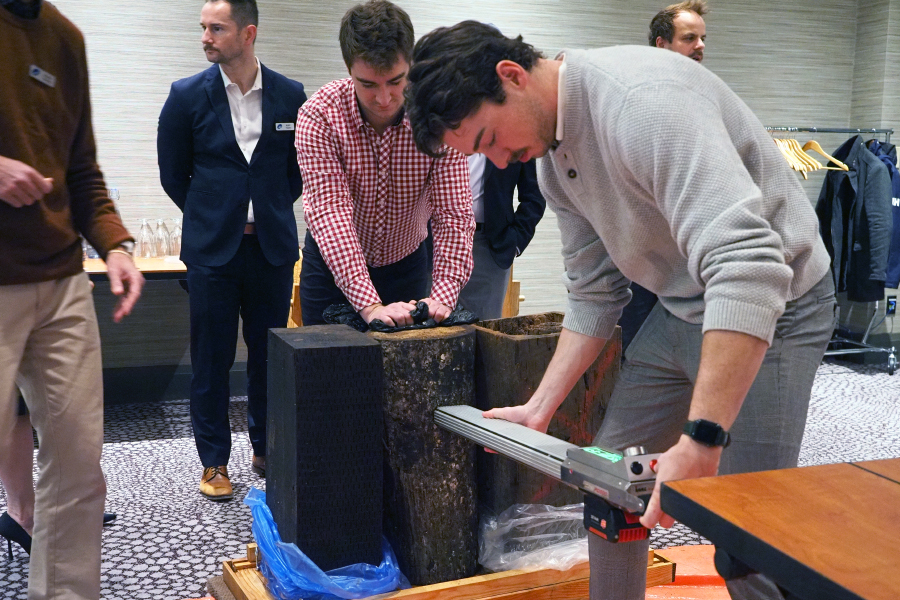
Bridge inspection and rehabilitation have been the backbone of Associated Engineering’s transportation structures services for over 40 years. Our team conducts visual inspections, structures modelling, and rehabilitation design to assist clients in preserving and extending the life of their bridges and structures inventory. We are constantly advancing the tools that we use for bridge inspections for specialized and non-destructive material testing.
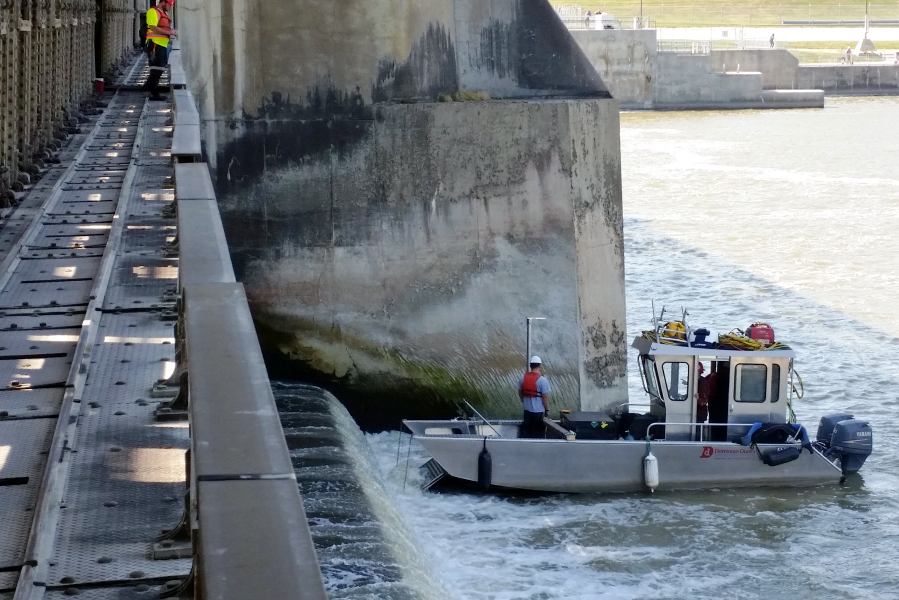
On recent projects, we have employed a wide array of innovative approaches and technologies for gathering data, conducting risk analysis, prioritizing work, visualizing recommendations, as well as identifying funding options. We have completed projects from BC to Ontario and the North, including detailed condition assessments of the historic St. Andrews Lock and Dam in Manitoba and Baxter Bridge in BC, and employed drones for improved data capture and specialized timber inspection tools.
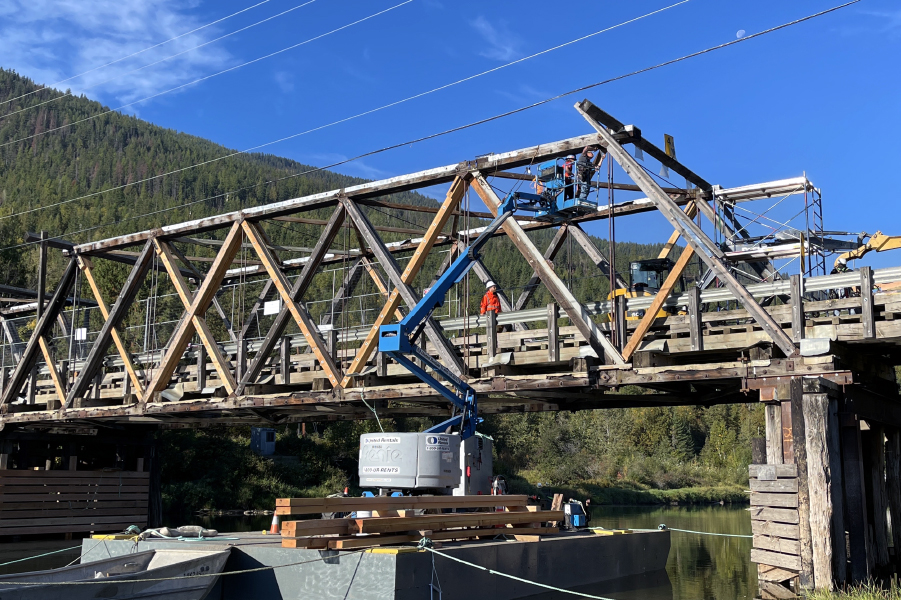
With aging infrastructure and competing needs for limited government funds, risk management, strategy, prioritization, and funding are critical considerations when establishing a bridge management approach. Owners need to undertake visual inspections, and consider bridge condition, required maintenance, repairs, rehabilitation or replacement, as well as public needs, risks, and the municipality’s overall funding.
For example, Associated Engineering has worked closely with Smoky Lake County in Alberta for almost 20 years, assisting them to manage their bridge inventory, comprising 88 bridges and culverts. A constant challenge has been securing adequate funding for bridge repairs and replacements. With approximately 4,000 residents, the County’s low tax base, large structures inventory, and recent escalating construction costs their challenges have compounded. Moreover, the County is facing aging infrastructure – many structures built between 1950 and 1970 now require immediate and significant rehabilitation.
Given these challenges, risk identification and rehabilitation prioritization are crucial. Decisions on keeping roads open or closed are based on traffic volumes, safety risks, and resident and business access needs. The County heavily relies on grant funding and provincial support, but faces competition from municipalities across the province for grants, which are often over-subscribed. Funding tends to be directed only to the most critical replacements.
To assist Smoky Lake County, Associated has supported lobbying efforts for funding key structures where closures would significantly impact the County’s economy. Identifying and targeting key assets and focusing efforts on securing funding for their maintenance and rehabilitation have been important components of the County’s bridge management strategy, and maintaining the network’s level of service through funding constraints. Our collective efforts have resulted in funding for crucial bridge replacements, that would not have been possible without our strategic approach.
Associated’s experience with the City of Kelowna showcases the benefits of a proactive bridge management strategy. We have assisted the City of Kelowna in managing their bridge inventory since the early 1990s, focusing initially on thorough inspections and detailed maintenance lists. These efforts identified repairs, rehabilitation, or replacement projects, following the BC Ministry of Transportation and Infrastructure‘s system.
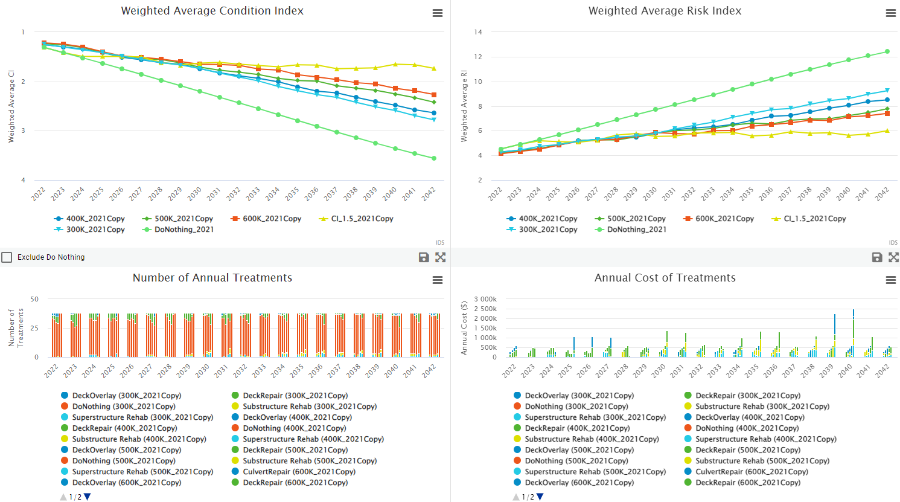
In 2018, we introduced a new inspection rating process for Kelowna. This innovative system assessed the condition of bridge elements and evaluated the relevancy of observed defects, measuring their impact on the structure’s performance. By developing a comprehensive risk profile for each bridge and its defects, we prioritized repairs based on the risk they posed to the City and its residents.
Incorporating factors such as Average Daily Traffic (ADT) allowed us to refine our prioritization further, ensuring funds are directed to the most critical projects. Over the past six years, this risk-based approach has enabled Kelowna to implement an aggressive bridge rehabilitation program. The condition of the city’s bridges has improved significantly, shifting from reactive to proactive maintenance strategies. This transformation not only enhances public safety, but also ensures the longevity and reliability of Kelowna’s bridge infrastructure.
The experiences of Smoky Lake County and the City of Kelowna underscore the importance of tailored strategies in bridge management. Whether facing funding challenges or managing a well-funded inventory, Associated’s ability to assess risks, prioritize, innovate, and strategically plan are critical to a bridge management approach that provides safe and reliable infrastructure for communities and delivers value to our clients.
About the Author:
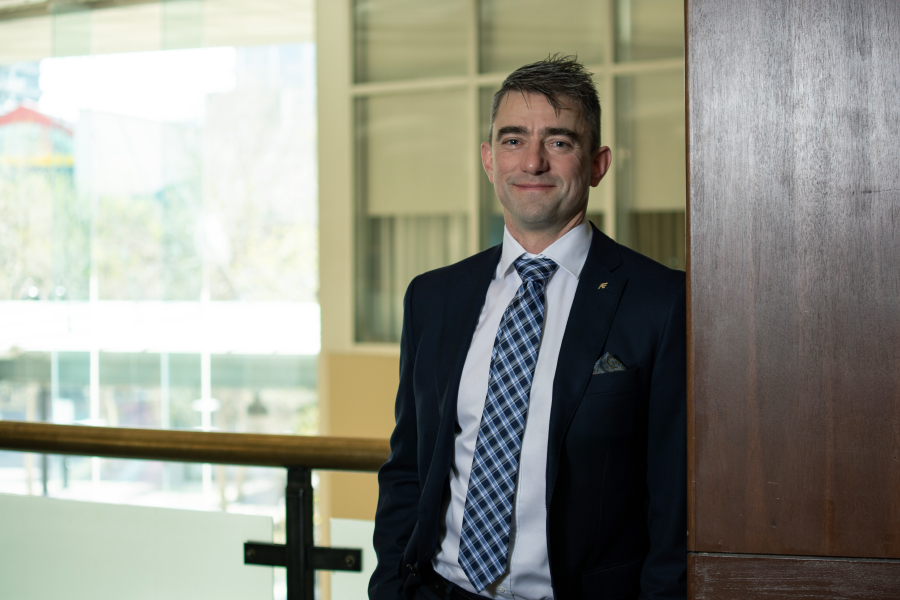
Michael Paulsen, M.Sc., P.Eng. is Vice President, Transportation Structures and a structural engineer with over 20 years of experience. He has been involved in a wide variety of projects, including roadway, pedestrian, heavy rail, and LRT bridges. Michael’s experience includes concept, preliminary and detailed design, project management, asset management, planning, load-ratings and bridge assessment studies.